Realiza inspecciones rutinarias y programadas de todos los equipos. Estas revisiones ayudan a identificar problemas antes de que se conviertan en fallos costosos. Utiliza listas de verificación para garantizar que cada aspecto crítico sea evaluado meticulosamente, desde componentes eléctricos hasta sistemas hidráulicos.
Implementa un sistema de mantenimiento predictivo. Utiliza tecnología avanzada como análisis de vibraciones y termografía para monitorear el estado de los equipos. Esto permite anticipar fallos y planificar reparaciones en momentos óptimos, minimizando tiempos de inactividad.
Crea una base de datos sobre el historial de mantenimiento. Lleva un registro detallado de las intervenciones realizadas, piezas reemplazadas y las condiciones de operación de cada máquina. Esta información resulta invaluable para identificar patrones y tomar decisiones informadas sobre el mantenimiento futuro.
Capacita a tu equipo. Asegúrate de que los operadores y el personal de mantenimiento estén bien entrenados en el uso correcto y el cuidado de los equipos. Proporciona formación continua para mantenerlos actualizados sobre las mejores prácticas y nuevos desarrollos en tecnología industrial.
Por último, promueve la cultura de seguridad. Realiza auditorías de seguridad regularmente y fomenta la comunicación abierta sobre posibles riesgos. Un entorno de trabajo seguro no solo protege a los empleados, sino que también prolonga la vida útil de los equipos.
Importancia del mantenimiento preventivo en la industria
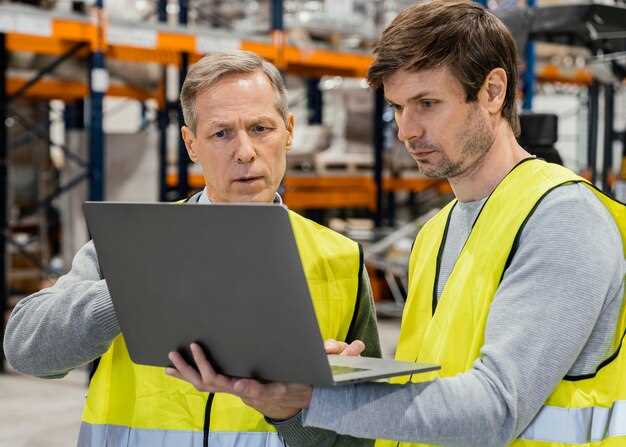
Implementar un programa de mantenimiento preventivo reduce significativamente el riesgo de fallas inesperadas. Adopta un enfoque proactivo que garantice la disponibilidad continua de los equipos. Esto no solo minimiza el tiempo de inactividad, sino que también optimiza el rendimiento de la maquinaria.
Beneficios clave del mantenimiento preventivo
- Extensión de la vida útil de los equipos: Un mantenimiento regular ayuda a identificar desgaste y realizar reparaciones antes de que se conviertan en problemas mayores.
- Reducción de costos: Prevenir fallos evita gastos imprevistos y costosos en reparaciones urgentes. Invertir en mantenimiento periódico se traduce en ahorro a largo plazo.
- Mejoras en la seguridad: Mantener equipos en condiciones óptimas minimiza accidentes laborales y lesiones. La seguridad es prioritaria en cualquier entorno industrial.
- Aumento de la eficiencia operativa: Los equipos bien mantenidos funcionan de manera más eficiente, mejorando la productividad general de la planta.
Implementación de un plan de mantenimiento
Desarrolla un cronograma basado en las recomendaciones del fabricante y las condiciones de operación. Incluye las siguientes actividades:
- Inspecciones regulares: Evalúa el estado de los equipos y verifica que todos los componentes funcionen correctamente.
- Mantenimiento programado: Realiza cambios de lubricantes, ajustes y reemplazos de piezas según un calendario predeterminado.
- Capacitación del personal: Asegúrate de que el equipo conozca las técnicas adecuadas para el cuidado y uso de los instrumentos y maquinaria.
- Registro de actividades: Documenta todas las intervenciones para facilitar la planificación futura y el análisis de fallas.
El mantenimiento preventivo maximiza la disponibilidad operativa y contribuye a un ambiente de trabajo seguro y productivo. Establece tu programa hoy y observa los beneficios a largo plazo.
Estrategias para la inspección regular de maquinaria
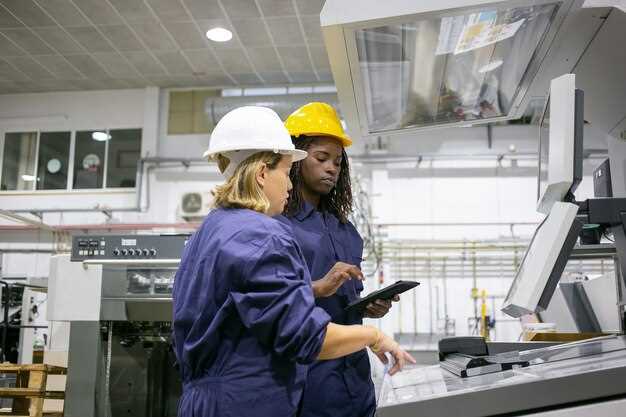
Implementa un calendario de inspección que defina claramente la frecuencia y los tipos de revisión necesarios para cada máquina. Esta práctica permite identificar problemas antes de que se conviertan en fallas mayores.
Incorpora listas de verificación detalladas que incluyan todos los componentes críticos. Las listas simplifican el proceso y aseguran que no se omita ningún aspecto importante durante la revisión.
Utiliza tecnologías de monitoreo en tiempo real. Sensores y sistemas de análisis de datos ayudan a detectar anomalías en el funcionamiento de las máquinas. Establece alertas automáticas para que el personal técnico pueda actuar de manera inmediata.
Capacita a tu equipo en la identificación de signos de desgaste o fallo. Un personal bien entrenado puede realizar evaluaciones más precisas y reportar cualquier irregularidad inmediatamente.
Registra todos los hallazgos y acciones tomadas durante las inspecciones. Un historial de mantenimiento permite entender patrones de fallos y mejora la toma de decisiones sobre el futuro del equipo.
Realiza auditorías regulares de los procedimientos de inspección para asegurarte de que se cumplen las normas establecidas. Esto garantiza que las estrategias implementadas siguen siendo efectivas y se ajustan a las necesidades cambiantes de la operación.
Cómo establecer un calendario de mantenimiento adecuado
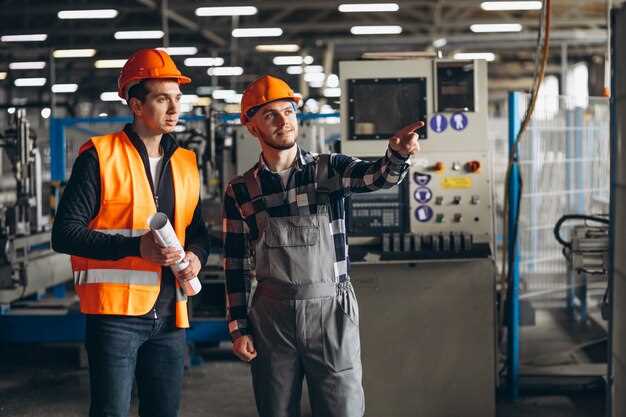
Evalúa primero la frecuencia de uso de cada equipo. Los dispositivos que operan a tiempo completo requieren un mantenimiento más regular que aquellos que funcionan de manera intermitente. Adapta las intervenciones según la carga de trabajo y las recomendaciones del fabricante.
Clasificación de equipos
Categoriza los equipos en grupos según su criticidad y el impacto potencial en la producción. Por ejemplo, las máquinas esenciales para la línea de producción deben tener un calendario más riguroso, mientras que el mantenimiento de equipos secundarios puede ser menos frecuente.
Documentación y seguimiento
Registra cada actividad de mantenimiento. Utiliza hojas de cálculo o software especializado para registrar las fechas, tareas realizadas y observaciones. Este historial ayuda a identificar patrones de fallos y ajustar el calendario según sea necesario.
Involucra a tu equipo en el proceso de planificación. Sus aportes facilitarán la identificación de problemas recurrentes y mejorarán la efectividad del mantenimiento. Programa reuniones periódicas para revisar el calendario y ajustarlo según la situación actual del equipo.
Finalmente, considera la estacionalidad en la producción. Ajusta los intervalos de mantenimiento en función de picos de demanda o paradas de producción programadas. Esta planificación garantiza un uso óptimo de los recursos disponibles.
Herramientas digitales para el seguimiento del mantenimiento
Implementa un software de gestión de mantenimiento computarizado (CMMS) para optimizar el seguimiento de las actividades de mantenimiento. Los CMMS permiten registrar órdenes de trabajo, programar tareas preventivas y gestionar inventarios de repuestos, facilitando el acceso a la información en tiempo real.
Considera usar aplicaciones móviles que complementen el CMMS. Estas aplicaciones permiten a los técnicos reportar el estado de las máquinas y registrar intervenciones directamente desde el lugar de trabajo, garantizando una actualización instantánea de los datos.
Incorpora sensores IoT en los equipos para recopilar datos relevantes sobre su funcionamiento. Estos dispositivos pueden monitorear temperatura, vibración y otros parámetros críticos, alertando a los operadores sobre posibles fallas antes de que ocurran.
Uso de plataformas de análisis de datos ayuda a interpretar la información recopilada. Estas herramientas permiten identificar patrones de fallas y determinar cuándo es necesario realizar el mantenimiento predictivo. Asegúrate de utilizar soluciones que integren inteligencia artificial para mejorar continuamente las predicciones.
Herramienta | Funcionalidad | Beneficios |
---|---|---|
CMMS | Gestión de órdenes de trabajo | Registro centralizado de actividades |
Aplicaciones móviles | Acceso a información en campo | Actualizaciones en tiempo real |
Sensores IoT | Monitoreo continuo de equipos | Detección de fallas proactivas |
Plataformas de análisis de datos | Análisis de patrones de fallas | Optimización de la programación de mantenimiento |
Formación en el uso de estas herramientas mejora la efectividad del personal y asegura el máximo aprovechamiento de la tecnología disponible. Realiza capacitaciones periódicas para mantener a todo el equipo actualizado sobre novedades y buenas prácticas.
Capacitación del personal en mantenimiento de equipos
Proporciona formación práctica. Realiza talleres donde los empleados puedan interactuar directamente con el equipo. Esto no solo refuerza el conocimiento teórico, sino que también mejora su confianza y habilidades técnicas.
Incorpora simulaciones de fallos. Esto permite que el personal experimente situaciones reales de falla bajo condiciones controladas. Con esta técnica, los trabajadores aprenderán a diagnosticar problemas y a implementar soluciones rápidas.
Establece un programa de certificación. Al final de un ciclo de formación, ofrece una certificación que valide las competencias adquiridas. Esto motiva a los empleados a comprometerse más con su desarrollo profesional.
Organiza sesiones de capacitación continua. Los avances en tecnología requieren un conocimiento actualizado. Programa capacitaciones regulares o acceso a cursos en línea para que el personal esté al día con las nuevas herramientas y procedimientos.
Involucra a los empleados en la creación de contenido formativo. Al pedir sus sugerencias y experiencias, generas un ambiente colaborativo y acogedor, donde se sienten valorados y motivados a compartir sus conocimientos.
Promueve la cultura de seguridad. Incluye aspectos de seguridad en cada sesión de capacitación. Asegúrate de que todos comprendan la importancia de seguir las normas y procedimientos de seguridad al trabajar con equipos industriales.
Finalmente, mide el impacto de la capacitación. Realiza encuestas y análisis post-capacitación para evaluar el desempeño del personal. Esto permitirá ajustar las futuras sesiones de formación, asegurando que sean aún más útiles y relevantes.
Identificación y gestión de piezas de repuesto críticas
Clasifica las piezas de repuesto según su impacto en la operación del equipo. Identifica aquellas que, al fallar, podrían causar paradas prolongadas o daños severos. Utiliza un sistema de codificación que facilite su identificación rápida, como códigos de colores o etiquetas descriptivas.
Realiza un inventario regular de las piezas críticas, registrando la cantidad disponible y el estado de cada una. Implementa un software de gestión que te permita llevar un control detallado y te alerte sobre los niveles bajos de stock.
Crea un plan de abastecimiento que contemple los plazos de entrega y la disponibilidad de proveedores confiables. Considera la opción de tener piezas en inventario que puedan ser necesarias de forma inmediata y que impacten en la continuidad operativa.
Establece relaciones sólidas con los proveedores de piezas de repuesto. Negocia contratos que incluyan tiempos de entrega garantizados y condiciones de servicio. Acceso rápido a estos recursos será fundamental en situaciones críticas.
Forma al personal en el manejo y cuidado de las piezas de repuesto. Instruye sobre la correcta instalación y mantenimiento para prolongar su vida útil. La capacitación asegura que las piezas se gestionen adecuadamente y se reduzcan los errores durante su uso.
Realiza una revisión periódica del rendimiento de las piezas críticas. Analiza las fallas y ajusta el plan de gestión según las tendencias y datos acumulados. La retroalimentación continua permitirá optimizar el stock y prevenir problemas futuros.
Mejoras en la documentación y registro de mantenimiento
Implementa un sistema de registro digital para el mantenimiento que centralice toda la información relevante. Utiliza software diseñado específicamente para este propósito, lo que facilita el acceso a datos históricos, cronogramas y cualquier actualización necesaria.
- Incluir detalles específicos: Registra la fecha, el tipo de mantenimiento realizado, quién lo llevó a cabo y los materiales utilizados. Esto permite un seguimiento claro y evita confusiones en el futuro.
- Fotografías y esquemas: Adjunta imágenes del equipo antes y después del mantenimiento. Esto ayuda a documentar los problemas y las soluciones implementadas.
- Feedback del operador: Después de cada intervención, recoge comentarios de los operadores sobre el funcionamiento del equipo. Esto influye en posibles ajustes en los futuros mantenimientos.
Establece un protocolo de revisión periódica de la documentación. Asigna responsabilidades claras a personas específicas para garantizar que la información se mantenga actualizada y precisa.
- Realiza auditorías semestrales de registros de mantenimiento.
- Capacita al personal en la importancia de una documentación adecuada y precisa.
- Corrige cualquier inconsistencia detectada durante las auditorías de inmediato.
Facilita el acceso a la documentación a través de dispositivos móviles para que el equipo, en cualquier momento, pueda consultar el historial y las especificaciones del equipo. Esto agiliza los procesos y reduce el tiempo perdido en la búsqueda de información.
- Integración con otros sistemas: Si es posible, integra el sistema de mantenimiento con otros softwares de gestión, como ERP o GMAO. Esta sinergia mejora la información y los datos analíticos.
- Informes automáticos: Configura el software para que genere informes automáticos sobre el estado de los equipos y sus mantenimientos programados, facilitando la planificación futura.
Con la implementación de estas mejoras, la documentación y el registro de mantenimiento se convierten en herramientas poderosas que apoyan la operación eficaz de los equipos industriales.
Consejos para la selección de proveedores de servicios de mantenimiento
Verifica la experiencia y referencias. Investiga la trayectoria del proveedor en la industria específica. Pide referencias de clientes anteriores y busca casos de éxito. La experiencia directa en tu tipo de equipo puede ser un indicativo de su capacidad para manejar tus necesidades.
Solicita certificaciones y credenciales. Comprueba que el proveedor cuente con las certificaciones requeridas, como ISO o similares, que avalan su conocimiento y calidad en los servicios ofrecidos. Esto asegura que operen bajo normativas reconocidas y estándares de calidad.
Evalúa la gama de servicios ofrecidos. Asegúrate de que el proveedor ofrezca un portafolio amplio, desde mantenimiento preventivo hasta reparaciones de emergencia. Esto permite flexibilidad y adaptación según las necesidades cambiantes de tu operación.
Obtén información sobre su disponibilidad. Un buen proveedor debe ofrecer atención 24/7, ya que el tiempo de inactividad puede afectar significativamente la producción. Pregunta por los tiempos de respuesta ante incidencias y el soporte técnico que brindan.
Analiza la comunicación y el servicio al cliente. La calidad en la comunicación es clave. Un proveedor que escucha y responde de manera clara y rápida facilitará el proceso de mantenimiento y resolverá problemas de forma más ágil.
Pide un presupuesto detallado. Un desglose claro de costos ayuda a evitar sorpresas desagradables. Compara precios de diferentes proveedores, pero también ten en cuenta la calidad del servicio que se ofrece a ese precio.
Considera el uso de tecnología. Pregunta si el proveedor utiliza herramientas y software avanzados para el seguimiento y gestión del mantenimiento. Esta práctica puede optimizar procesos y mejorar la planificación de las intervenciones.
Consulta sobre formación y capacitación. Verifica si el personal del proveedor recibe formación continua. Esto garantiza que estén al día con las últimas tecnologías y metodologías en mantenimiento industrial, lo que se traduce en un servicio más competente.
Video:
Entrevista a tecnico de mantenimiento
Entrevista a tecnico de mantenimiento by Simon Leon 37,705 views 6 years ago 4 minutes, 23 seconds
Pregunta-respuesta:
¿Cuáles son las prácticas más comunes para el mantenimiento de equipos industriales?
Las prácticas más comunes incluyen el mantenimiento preventivo, en el cual se realizan inspecciones y ajustes regularmente para prevenir fallos, y el mantenimiento correctivo, que se lleva a cabo después de que un equipo presenta un problema. También es fundamental llevar un registro detallado del mantenimiento realizado y utilizar técnicas como el análisis de vibraciones y la termografía para detectar problemas antes de que se conviertan en fallos graves.
¿Cómo puedo implementar un programa de mantenimiento preventivo en mi empresa?
Implementar un programa de mantenimiento preventivo requiere varios pasos. Primero, se debe realizar un inventario de todos los equipos industriales y sus especificaciones técnicas. Luego, se debe definir un calendario de mantenimiento basado en las recomendaciones del fabricante y las condiciones de operación de los equipos. Es recomendable involucrar a los operarios que usan los equipos, ya que su experiencia puede proporcionar información valiosa. Por último, es importante establecer un sistema de seguimiento para evaluar la efectividad del programa y realizar ajustes cuando sea necesario.
¿Qué herramientas son recomendables para el mantenimiento de equipos industriales?
Las herramientas recomendadas para el mantenimiento de equipos industriales incluyen medidores de vibraciones, termómetros infrarrojos, multímetros, y herramientas de limpieza específicas. También se pueden considerar sistemas de gestión de mantenimiento asistido por computadora (CMMS) que ayudan a programar y llevar un control del mantenimiento realizado, así como software de monitoreo que permite supervisar el estado de los equipos en tiempo real. La elección de las herramientas dependerá del tipo de maquinaria y de las necesidades específicas de mantenimiento de cada empresa.
¿Qué importancia tiene la capacitación del personal en el mantenimiento de equipos industriales?
La capacitación del personal es clave para el mantenimiento exitoso de equipos industriales. Un personal bien entrenado puede identificar problemas en etapas tempranas, realizar el mantenimiento adecuado y evitar daños costosos a los equipos. Además, la capacitación fomenta una cultura de seguridad en el trabajo, ya que los trabajadores conocen los procedimientos adecuados y los riesgos asociados con el mantenimiento. También se requiere formación continua para mantenerse al tanto de las nuevas tecnologías y métodos de mantenimiento que puedan surgir en la industria.
¿Cómo pueden las tecnologías avanzadas mejorar el mantenimiento industrial?
Las tecnologías avanzadas, como la inteligencia artificial y el análisis de datos, pueden mejorar significativamente el mantenimiento industrial. Estas tecnologías permiten realizar análisis predictivos que ayudan a anticipar fallos en los equipos antes de que ocurran, lo que reduce el tiempo de inactividad y los costos de reparación. Además, el uso de sensores IoT (Internet de las Cosas) permite el monitoreo en tiempo real del estado de los equipos, proporcionando datos valiosos que pueden ser utilizados para optimizar las intervenciones de mantenimiento. La implementación de estas tecnologías también puede facilitar una mejor planificación y programación del mantenimiento.
¿Cuáles son algunas de las mejores prácticas para el mantenimiento de equipos industriales?
Algunas de las mejores prácticas incluyen la implementación de un programa de mantenimiento preventivo, la capacitación continua del personal de mantenimiento, la utilización de tecnología para el monitoreo de equipos y la documentación rigurosa de todas las actividades de mantenimiento. Un programa preventivo ayuda a identificar problemas antes de que se conviertan en fallos, mientras que la formación asegura que el personal esté al tanto de los últimos avances y técnicas en mantenimiento.
¿Por qué es importante documentar las actividades de mantenimiento en equipos industriales?
Documentar las actividades de mantenimiento es fundamental porque proporciona un historial claro de las intervenciones realizadas en cada equipo. Este registro permite a los técnicos identificar patrones de fallos, planificar adecuadamente las paradas de mantenimiento y tomar decisiones informadas sobre mejoras o reemplazos. Además, una buena documentación facilita la auditoría y el cumplimiento de normativas, garantizando que la empresa cumpla con los estándares de seguridad y calidad establecidos por la industria.