La integración de tecnologías avanzadas está transformando la manera en que operan los sectores productivos. Se trata de un cambio profundo que afecta tanto a procedimientos como a la eficiencia general. Empresas adoptan nuevas herramientas que permiten optimizar recursos y reducir costos.
Las fábricas del futuro están conectadas de forma inteligente. Máquinas y sistemas interactúan ahora con una precisión inimaginable hace unas décadas. Este fenómeno abre oportunidades impresionantes para el crecimiento y la innovación. Procesos antes complejos se simplifican gracias a la conectividad y el análisis de datos en tiempo real.
Motores inteligentes, sensores avanzados y redes interconectadas forman la columna vertebral de esta evolución en la manufactura. Las plantas modernas ya no solo producen. También recopilan, analizan y actúan basado en una gran cantidad de información. Las decisiones se toman con mayor exactitud y rapidez. Como resultado, se minimizan errores y se maximizan los beneficios.
Transformar plantas y fábricas en ecosistemas conectados ha dejado de ser una opción para convertirse en una necesidad. Las mejoras tecnológicas permiten a las empresas ser más competitivas. La eficiencia no es la única ganancia; la sostenibilidad también juega un papel crucial. Reducir el desperdicio y optimizar el uso de materias primas son ventajas adicionales que hacen esta transición indispensable.
El Impacto del IoT en la Automatización Industrial
La integración de tecnologías interconectadas ha transformado significativamente la producción en fábrica. Equipos y máquinas ahora se comunican entre sí. Esta interacción mejora la eficiencia operativa. Se agilizan las tareas repetitivas y se disminuyen errores. Implementar estas soluciones permite un mayor control y supervisión. Todo esto contribuye a un rendimiento óptimo.
La mayor visibilidad en tiempo real es un beneficio clave. Permite una toma de decisiones más precisa. Monitorear los procesos en directo reduce tiempos de inactividad. Esto maximiza la productividad. La información recolectada facilita el mantenimiento predictivo. Los ingenieros pueden anticipar y resolver problemas antes de que surjan, evitando interrupciones costosas y prolongadas.
Otro aspecto crucial es la seguridad mejorada. Sistemas inteligentes detectan y reaccionan ante anomalías rápidamente. Este monitoreo constante protege los activos críticos. Además, se minimizan los riesgos para los trabajadores. La salud y la seguridad son prioritarias en entornos modernos.
Beneficio | Descripción |
---|---|
Visibilidad en tiempo real | Monitoreo continuo que facilita decisiones informadas y precisas. |
Mantenimiento predictivo | Anticipación y solución de problemas antes de que ocurran. |
Seguridad mejorada | Detección rápida de anomalías y reducción de riesgos laborales. |
En conclusión, la incorporación de estas tecnologías en fábricas y plantas trae consigo cambios profundos. Los beneficios son evidentes. La producción se vuelve más eficiente, segura y rentable. Es un paso necesario hacia el futuro de la industria. Cada día, las empresas descubren nuevas ventajas y posibilidades.
Transformación de Procesos Productivos
La evolución tecnológica ha dado lugar a numerosos avances. Hoy nos encontramos en un punto de inflexión. Esto ha permitido una mayor eficiencia. También ha traído consigo múltiples retos. Empresas de todo el mundo buscan adaptarse. Las transformaciones son inevitables y necesarias. Con la adopción de nuevas tecnologías, los procesos productivos han experimentado una metamorfosis sin precedentes.
La digitalización ha cambiado la forma de operar. Ahora, las industrias cuentan con herramientas más precisas. Estas permiten a los operadores obtener datos en tiempo real. Las decisiones se toman basadas en información concreta.
- Mayor control de calidad.
- Optimización de recursos.
- Reducción de desperdicios.
- Menor tiempo de producción.
Además, la interconexión entre máquinas y sistemas permite un flujo constante de información. Esto no solo mejora el rendimiento, sino también la seguridad laboral. Los empleados pueden adelantarse a fallos potenciales. Las empresas, por lo tanto, son más competitivas.
Otra ventaja es la personalización masiva. Las fábricas adaptan sus líneas de producción. Se atienden pedidos específicos de los clientes. La flexibilidad es un factor clave. Los consumidores demandan productos únicos.
Los sistemas modernos también han permitido el desarrollo de modelos predictivos. Los operarios pueden prever el mantenimiento de maquinaria. Así, se evitan costosos tiempos de inactividad. La producción se mantiene constante y fluida.
En definitiva, cada sector ha aprovechado estos cambios a su manera. Se observa una sinergia entre tecnología y operativa. La implementación estratégica de estas herramientas ha resultado en procesos más ágiles y eficientes. El futuro es prometedor y lleno de oportunidades para quienes se adapten con rapidez.
Optimización de la Cadena de Suministro
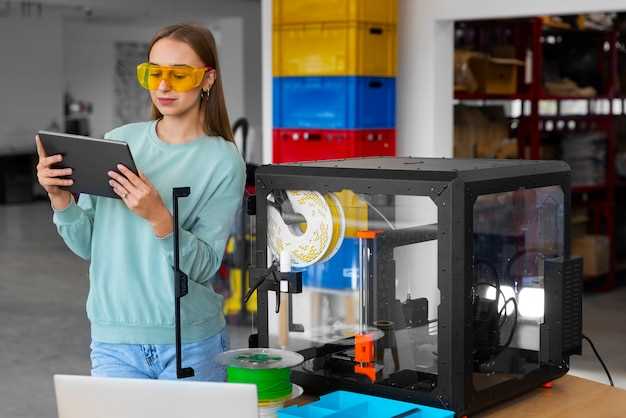
La cadena de suministro se ha transformado en una red inteligente. Con la integración de tecnologías avanzadas, estamos viendo un enorme avance en la mejora de procesos logísticos. Esto se refleja en mayor eficiencia y reducción de errores. Las empresas ahora pueden anticiparse a problemas antes de que ocurran.
Las soluciones tecnológicas ofrecen beneficios claros:
- Mejor gestión de inventarios.
- Reducción del tiempo de inactividad.
- Menor costo operativo.
- Mayor trazabilidad de productos.
Al emplear datos en tiempo real, se logra una reacción inmediata frente a cualquier inconveniente. Un sistema bien optimizado permite una visibilidad total a lo largo de la cadena. Esto significa que los gerentes pueden tomar decisiones fundamentadas rápidamente.
El flujo de información es constante. El intercambio de datos entre dispositivos y sistemas es preciso. Esta continuidad en la comunicación minimiza riesgos y maximiza oportunidades de mejora.
Además, el análisis predictivo juega un papel crucial. Con la capacidad de prever demandas y ajustar el suministro, las empresas logran mantener un equilibrio perfecto entre oferta y demanda, optimizando la capacidad de almacenamiento y reduciendo el desperdicio.
- Anticipación de la demanda.
- Planificación eficiente.
- Eliminación de cuellos de botella.
En conclusión, la integración de estas tecnologías en la cadena de suministro permite a las empresas ser más ágiles. La eficiencia y la productividad aumentan significativamente, dando lugar a una operación más competitiva y rentable. Está claro que estos avances están redefiniendo la manera en que las organizaciones manejan sus procesos logísticos.
Minimización de Errores Humanos
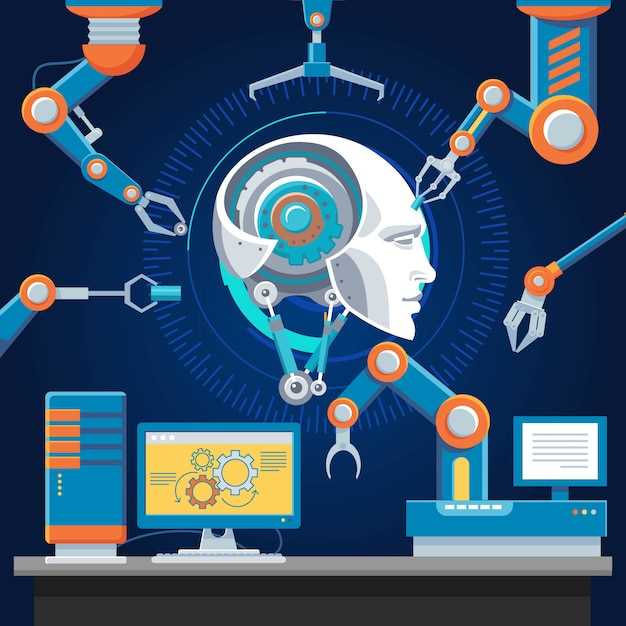
En la industria moderna, reducir las equivocaciones humanas es crucial. Las fallas pueden ser costosas. Afectan la seguridad y la calidad. Desvían el rendimiento, generando consecuencias negativas. Minimizar estas faltas tiene beneficios enormes. Tecnología avanzada ofrece soluciones increíbles y precisas.
Las nuevas tecnologías permiten monitoreo continuo. Sistemas inteligentes supervisan tareas en tiempo real. Esto asegura que los procesos se cumplan correctamente. La intervención humana se limita a la supervisión, reduciendo así los potenciales fallos. Además, se pueden implementar alarmas que avisen ante cualquier anomalía.
Beneficios | Descripción |
---|---|
Mejor Precisión | Los sistemas automatizados llevan a cabo tareas repetitivas con mayor exactitud, disminuyendo las probabilidades de error. |
Aumento de la Seguridad | Reducir la participación humana en procesos peligrosos disminuye el riesgo de accidentes. |
Optimización del Tiempo | Las tareas se completan más rápido gracias a la eficiencia de las máquinas, permitiendo a los trabajadores enfocarse en trabajos más complejos y creativos. |
Costos Reducidos | Menos errores implican menos pérdidas de material y tiempo, resultando en una reducción significativa de costos operativos. |
Implementar estas tecnologías también facilita la capacitación. Los trabajadores pueden aprender a manejar sistemas de supervisión y control. Esto no solo reduce errores, sino que también mejora sus habilidades. Además, permite la recopilación de datos valiosos. El análisis de estos datos contribuye a la toma de decisiones informada, optimizando los procesos en el futuro. En resumen, la minimización de errores humanos no es solo un objetivo, es una realidad alcanzable con la tecnología moderna.
Incremento de la Eficiencia Operacional
Las nuevas tecnologías están cambiando profundamente el panorama de muchas industrias. Un aspecto clave es cómo mejoran la eficiencia. El rendimiento operativo se ve favorecido por sistemas avanzados. La recopilación y análisis de datos optimiza procesos. Cada componente en la cadena de producción se monitorea en tiempo real. Decisiones informadas se toman al instante, permitiendo ajustes precisos. La gestión de recursos se vuelve más efectiva, reduciendo costos y desperdicios.
Además, la previsión de problemas antes de que ocurran es ahora una realidad. No solo se automatiza la producción, sino también el mantenimiento preventivo. La información detallada permite reaccionar rápidamente ante cualquier irregularidad. Este nivel de control proporciona una ventaja competitiva significativa. Ya no es necesario depender de inspecciones manuales o estimaciones imprecisas. Todo está al alcance de un botón, fácil y accesible.
La integración de dispositivos inteligentes permite un seguimiento minucioso. A continuación, se presentan algunos beneficios clave:
Beneficio | Descripción |
---|---|
Reducción de costos | Minimiza el uso innecesario de materiales y energía. |
Optimización de procesos | Identifica y elimina cuellos de botella en la producción. |
Mantenimiento predictivo | Anticipa fallos antes de que afecten la operación diaria. |
Mayor seguridad | Detecta condiciones peligrosas y activa protocolos de respuesta. |
Flexibilidad | Permite adaptar la producción a cambios en la demanda. |
Cada uno de estos beneficios contribuye a un entorno de trabajo más ágil. La eficiencia no solo se mide en términos de velocidad, sino también en calidad. Los errores se reducen considerablemente. El resultado es un sistema integrado que responde eficazmente a cualquier desafío. Navegar en un mercado competitivo requiere innovación continua, y estas soluciones son el camino a seguir. Con cada avance, se abren nuevas oportunidades para mejorar la eficiencia operacional.
Mantenimiento Predictivo
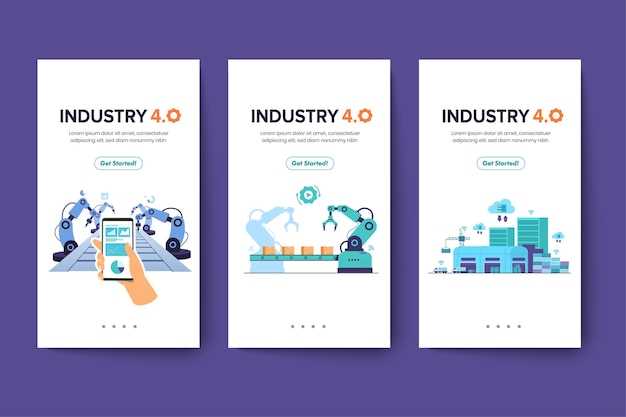
El mantenimiento predictivo se ha convertido en una práctica esencial en la industria. Busca anticiparse a las fallas, minimizando interrupciones inesperadas. Permite planificar intervenciones en el momento adecuado. Más eficiencia y menos tiempo de inactividad. No más sorpresas desagradables.
A continuación, algunas ventajas del mantenimiento predictivo:
- Reducción de costos:Evita reparaciones de emergencia, lo que ahorra dinero.
- Optimización de recursos:El personal trabaja de manera más efectiva.
- Aumento de la seguridad:Menos fallos significa menos riesgos para los trabajadores.
El mantenimiento preventivo y correctivo ya no son suficientes. Se necesita algo más. Aquí es donde entra el mantenimiento basado en el análisis de datos. Sensores y sistemas de monitoreo funcionan en conjunto. Recopilan información en tiempo real. Esta información se analiza de forma continua. Permiten detectar patrones de comportamiento anómalo. Anticipan problemas antes de que ocurran.
Metodologías empleadas en el mantenimiento predictivo:
- Monitoreo de condiciones:Evaluación constante del estado de equipos.
- Análisis de vibraciones:Detección de desequilibrios y desgastes.
- Termografía:Identificación de puntos calientes que indican posibles fallos.
- Ultrasonido:Escucha de ruidos inapreciables al oído humano.
Una planificación adecuada garantiza que las máquinas operen al máximo rendimiento. Las decisiones se basan en datos concretos. No depende de conjeturas ni de la experiencia subjetiva. Mayor eficacia al usar las herramientas adecuadas. Además, se alarga la vida útil de los equipos. Un entorno de trabajo más seguro.
En resumen, el mantenimiento predictivo transforma la gestión de activos. Mejores decisiones, equipos más confiables, y un ambiente de trabajo más seguro. Sin duda, una clave para el futuro de la industria moderna.
Reducción de Costos Operativos
La integración de tecnologías conectadas permite disminuir los gastos vinculados a las operaciones diarias. Equipos más eficientes y procesos optimizados contribuyen notablemente a esta economía. Todo lo que se necesita para mejorar la rentabilidad es hacer ajustes precisos y emplear soluciones tecnológicas inteligentes. Lograr una reducción significativa de costos no solo impacta en los beneficios económicos, sino también en la competitividad.
Una de las principales ventajas es la capacidad de monitorear equipos en tiempo real. Esto permite detectar fallas antes de que ocurra una avería mayor. El mantenimiento predictivo se convierte así en una herramienta poderosa. Se minimizan las interrupciones en la producción y se alarga la vida útil de la maquinaria. Con esta estrategia, las empresas pueden planificar adecuadamente sus recursos y evitar gastos imprevistos.
Por otro lado, la eficiencia energética es otro factor crucial. Sistemas inteligentes gestionan el consumo de electricidad, agua y otros recursos. Se disminuye el desperdicio de materiales y se optimizan los procesos productivos. Un mejor uso de los recursos se traduce en menores costos operativos y en una operación más sostenible.
Además, la recopilación y análisis de datos en tiempo real facilitan la toma de decisiones informadas. Información precisa permite identificar áreas de mejora y realizar ajustes necesarios en el momento adecuado. Empresas con acceso a estas tecnologías pueden anticiparse a cambios en la demanda o en las condiciones del mercado. Se reducen así los riesgos financieros y se incrementa la capacidad de adaptación.
En resumen, adoptar estas soluciones permite a las empresas no solo ahorrar dinero. También pueden mejorar su eficiencia y sostenibilidad. La clave está en implementar tecnologías que ofrezcan un control total sobre los diferentes aspectos operativos. De esta manera, se logra una gestión más eficiente y racional de los recursos disponibles.
La Industria y el Internet de las Cosas
La relación entre la manufactura y las tecnologías conectadas está transformando todo. Estos avances cambian cómo se gestionan las fábricas. No se trata solo de máquinas más eficientes. Es una sinergia entre tecnología y producción. Procesos que antes eran lentos ahora son inmediatos.
En las plantas modernas, todo se conecta. Sensores monitorean cada movimiento. Unidades de producción interactúan entre sí. La información fluye sin interrupciones. No hay espacio para errores humanos. Los dispositivos inteligentes comunican datos valiosos en tiempo real, permitiendo ajustes inmediatos y optimizando la continuidad operativa.
El futuro de la fabricación se define aquí. Innovar no es opcional. Empresas que adoptan estas tecnologías lideran el mercado. Aquellas que no lo hagan, quedarán rezagadas. Monitorear y ajustar los procesos productivos es esencial. Ayuda a reducir costos y a mejorar la calidad. Se crean productos más competitivos. Además, la seguridad laboral mejora.
La estrategia no solo se basa en la tecnología. También incluye la formación continua del personal. Todos deben estar preparados. Este ecosistema es complejo y multifacético. Equipos técnicos bien entrenados son cruciales para el éxito. Todo esto propicia un entorno de trabajo más seguro y eficiente.
Casos de éxito abundan. Empresas en todo el mundo han demostrado las ventajas. Aumento de eficiencia, reducción de errores. Producción más rápida. Es necesario estar siempre a la vanguardia tecnológica. La integración de estas tecnologías redefine la industria contemporánea. Y lo que antes parecía futurista, ahora es una realidad tangible. La relación entre el mundo físico y digital jamás ha sido más estrecha.
Integración de Dispositivos Inteligentes
La interacción entre dispositivos avanzados permite una conectividad nunca antes vista. Equipos interconectados comparten datos en tiempo real. Las máquinas trabajan eficientemente juntas. Pero, ¿cómo se logra esta conexión? La respuesta radica en la implementación estratégica de tecnología avanzada que permite la comunicación entre diferentes componentes.
Primero, los sensores inteligentes juegan un papel crucial. Estos pequeños dispositivos recopilan información esencial. Luego, la envián a unidades centrales. Pero esto no es todo, también es vital considerar las interfaces de usuario. La facilidad de uso es clave para la adopción de estas soluciones.
Además, la compatibilidad entre dispositivos de diferentes fabricantes añade un nivel de complejidad. Las empresas deben asegurarse de que sus sistemas pueden “hablar” entre sí. Esto no es una tarea fácil, requiere planificación y pruebas exhaustivas. Sin embargo, una vez lograda esta sinergia, los beneficios son inmensos.
Por supuesto, la seguridad es otro aspecto crucial. Al conectar diversos dispositivos, se aumenta la superficie de ataque. Por lo tanto, se deben implementar medidas de ciberseguridad robustas. Utilizar encriptación y actualizar regularmente el software son prácticas esenciales para proteger la integridad de los datos y el funcionamiento del sistema.
Vídeo:
La Automatización en la Nube: Revolucionando el Futuro
La Automatización en la Nube: Revolucionando el Futuro by Learn Automation2x 33 views 5 days ago 21 minutes
Preguntas y respuestas:
¿Qué es el Internet de las Cosas (IoT) y cómo se aplica en la automatización industrial?
El Internet de las Cosas (IoT) se refiere a la interconexión de dispositivos y sistemas a través de internet, permitiendo la comunicación y el intercambio de datos entre ellos. En la automatización industrial, IoT se aplica integrando sensores, actuadores y sistemas de control en equipos y máquinas, lo que permite monitorizar y gestionar operaciones en tiempo real. Con IoT, las fábricas pueden optimizar procesos, reducir tiempos de inactividad y mejorar la eficiencia productiva.
¿Qué es IoT y cómo se relaciona con la automatización industrial?
El Internet de las Cosas (IoT, por sus siglas en inglés) se refiere a la interconexión de dispositivos y máquinas a través de internet, permitiendo que se comuniquen entre sí y compartan datos. En el contexto de la automatización industrial, IoT permite la integración de sensores, actuadores y otros dispositivos en los sistemas de producción, facilitando el monitoreo y control en tiempo real, lo que optimiza los procesos y mejora la eficiencia de la planta.
¿Cuáles son algunos ejemplos específicos de cómo IoT está mejorando la eficiencia en la industria?
Existen numerosos ejemplos de IoT mejorando la eficiencia industrial. Un caso común es el mantenimiento predictivo, donde los sensores IoT monitorean el estado de las máquinas en tiempo real y predicen fallas antes de que ocurran. Esto reduce el tiempo de inactividad y los costos de reparación. Otro ejemplo es el monitoreo de la cadena de suministro, donde los dispositivos IoT rastrean las mercancías en tránsito, optimizando rutas y tiempos de entrega.
¿Qué desafíos enfrenta la implementación de IoT en la automatización industrial?
La implementación de IoT en la automatización industrial presenta varios desafíos. Uno de los más importantes es la seguridad cibernética, ya que la interconexión de dispositivos aumenta la superficie de ataque para los cibercriminales. Además, la integración de tecnologías IoT con sistemas heredados puede ser compleja y costosa. La administración y análisis de grandes volúmenes de datos generados por IoT también requieren infraestructura y experiencia especializada.